All You Need to Know About Aluminum Stamping, Stainless Steel Stamping, Pressure Die Casting, and CNC Bending
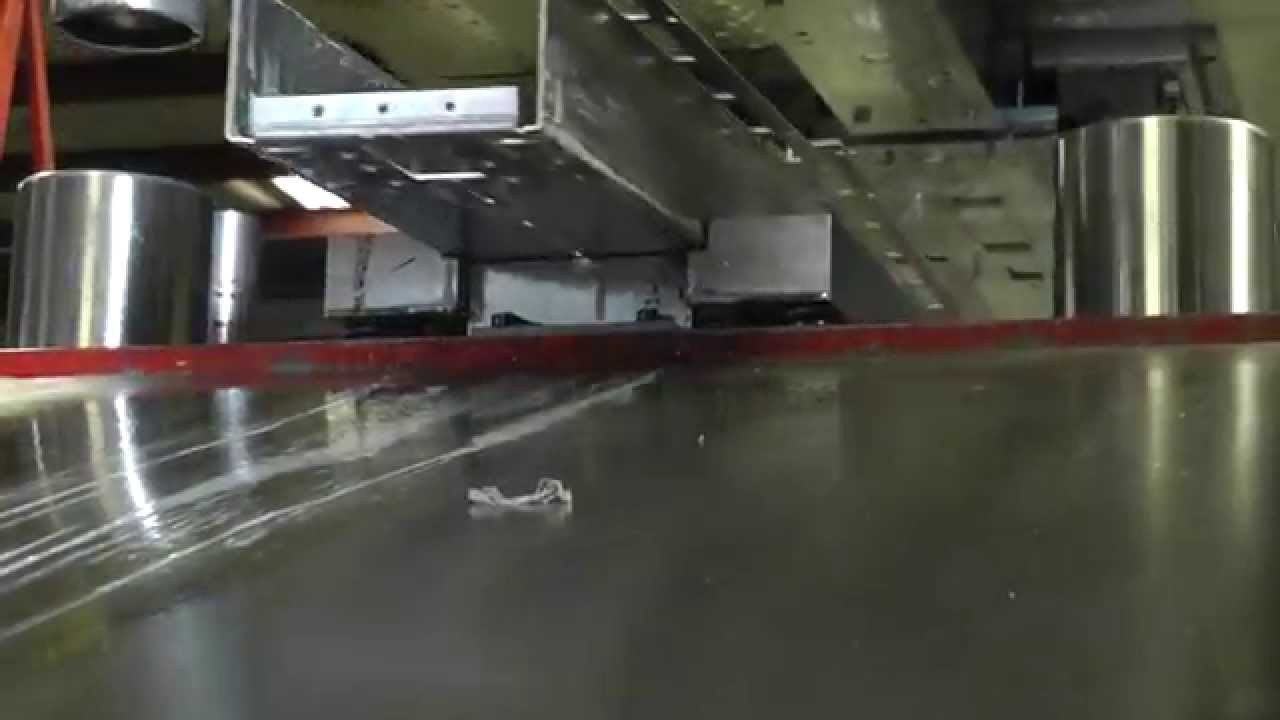
The metal stamping process converts flat sheets of metal into different shapes. Stamping is also known as pressing. To obtain a new shape out of a flat sheet, the flat metal sheet is placed in either blank or coil form into the stamping press. Forming tools and the die surface helps convert metals into a specific shape in the stamping press. Aluminum is one of the most common materials used for stamping. Aluminum is known for its workability and strength. We can find various use cases of aluminum stamping components in almost all industries.
Aerospace, marine, medical, electronics, and automotive industries need OEM aluminum stamping the most. In this comprehensive guide, you will learn about the aluminum stamping process, its use cases, properties, etc. We will also take a look at other options, like stainless steel stamping. You will also learn about other things like pressure die casting, CNC bending, diffusion welding, and high precision CNC machining.
Aluminum Stamping and the Most Common Aluminum Alloys
Usually, untreated aluminum is blended with other types of metals for enhancing or adding specific metal properties. It helps in improving the final product’s performance. The most common alloying materials are iron, magnesium, copper, zinc, silicon, and magnesium. All alloys have unique 4-digit numbers. The primary blending element determines the first alloy digit.
For instance:
- 1xxx for 99% untreated aluminum without alloying elements
- 2xxx for the aluminum blended with the copper
- 3xxx for aluminum blended with the manganese
- 4xxx for aluminum blended with the silicon
- 5xxx for aluminum blended with the magnesium
- 6xxx for aluminum blended with silicon and magnesium
- 7xxx for aluminum blended with the zinc
- 8xxx for aluminum blended with others
There may also be one letter at the end of the 4-digit number. This letter shows the temper designation of the metal alloy. For instance, aluminum stamping factories use F for ‘fabricated’, O for ‘annealed’, H for ‘strain hardened’, W for solution heat-treated, and T for heat treated.
What Are the Most Common Aluminum Alloys That Metal Stamping Companies Use?
Let’s take a look at the most common aluminum alloys that an aluminum stamping factory prefers for their use cases:
1100
This is a commercial untreated aluminum with high ductility, workability, and material softness. It is the perfect choice for applications that involve complex product or part design. These may include decorative or flatware components.
3003
It is an aluminum-manganese alloy. It is better than 1100 aluminum in strength. Moreover, 3003 also exhibits better workability and corrosion resistance. The most common use cases of 3003 include chemical handling items, cooking instruments, and kitchen equipment.
5052
It is an aluminum-magnesium alloy. 5052 exhibits better strength than all other non-heat-treated variations. Moreover, it offers better corrosion resistance, good finishing and workability characteristics, and improved fatigue strength. The most common use cases of 5052 include home appliances, heavy-duty cooking apparatuses, and aircraft parts.
6061
It is a heat-treatable aluminum alloy. Various advantageous chemical and mechanical properties of 6061 make it highly versatile. It is known for its exceptional weldability, formability, and corrosion resistance. 6061 is an ideal choice to make structural parts, like frames and bodies of automobiles.
What are the Common Aluminum Alloys Properties?
Aluminum stamping alloys may exhibit dissimilar properties according to their composition. However, the material group has a few shared properties that include:
- Higher strength-to-weight ratio
- Malleability and flexibility
- Low-temperature resistance
- Corrosion resistance
- Thermal and electrical conductivity
- Shiny and smooth finish with no or a little maintenance
Various manufacturers create aluminum alloys for different use cases. Some also offer wholesale aluminum stamping for different industries.
Stainless Steel
Stainless steel is tight to cut and form. However, it also depends on the stainless type you are working with and also what shape you want to make. For example, you must know the unique behavior of stainless steel for stainless steel stamping. Most stampers failed to cut and form stainless steel engineered for the flat carbon steel. A stainless steel stamping manufacturer must understand the material’s mechanical ability. The process design must be according to the behavior of the material.
Here, it is important to remember that high-temperature and corrosion-resistant steel is known as stainless steel. The oxide film rich in chromium is the reason behind the good resistance. The normal carbon steel, when you expose it to moisture, will corrode and form rust or an iron oxide brownish layer.
There are hundreds of specialty stainless steel types. Some stainless steels are ideal for high corrosion resistance. However, many others are known for withstanding higher heat. Some offer both benefits. A stainless steel stamping parts factory also adds alloys like nickel to the stainless steel for achieving specific desired properties.
Stainless Steel Use Cases
There are thousands of use cases of stainless steel. From marine screws to pocket knives to kitchen sinks, stainless steel is almost everywhere. Flatware is the most common stainless steel item that you can find in every retail store. The three grades are ‘good’, ‘better’, and the ‘best’. The nickel amount is what separates these three grades, giving it brilliance and luster. Take a quick look at the following details for stainless steel grating.
- Good stainless steel: Usually 18% chrome and 0% nickel
- Best stainless steel: Usually 18% chrome and 10% nickel
You will get different stainless steel stamping quotes depending on the stainless steel grade. Stainless steel is a perfect choice for products like surgical tools and pocket knives because of its higher carbon composition. Carbon helps the steel become hardened with the heat-treating process.
Other stainless steel types, like kitchen sink stainless steel, have little carbon content. Low carbon results in more stretchable, softer material. The automotive industry is one of the most common industries using stainless steel. An automobile’s exhaust is a classic example of high-temperature stainless steel grade.
Basic Types of Stainless Steel
The stamping industry uses three basic steel types, martensitic, ferritic, and austenitic. Let’s take a quick look at these types for a better understanding.
Austenitic
This stainless steel type is a perfect grade for use cases, such as deep drawing. Typically, this grade comprises lower carbon, making it perfectly suitable to make items like fat fryers, kitchen sinks, and deeply formed components or parts.
It is not possible to harden austenitic grade in stainless steel stamping with treating. However, it is possible to achieve this through cold treating the metal. This grade contains nickel and chromium, and also alloys in small amounts. It exhibits the best formability among all grades.
304L and 304 (normally extremely low carbon) and 316L and 316 (marine grades) are the most common austenitic grade stainless steel types. This stainless type is annealed state.
Ferritic
The automotive manufacturing industry requires a grade that is both heat and corrosion-resistant. Therefore, the ferritic grade becomes the most ideal choice for this industry. Ferritic grades may also exhibit exceptional formability according to the availability of alloys and carbon. Dissimilar to the austenitic grade, the ferritic grade doesn’t contain nickel.
These grades are magnetic and appropriate for drawing. The most common use cases of the ferritic grade include dryers, dishwashers, and exhaust systems of the automobile. 409, 430, and 439 are the most typical ferritic grade stainless steel types.
Martensitic
This stainless steel type is very much like the ferritic grade. However, there is one big difference. The martensitic grade stainless steel comes with a greater carbon amount. Because of this, it becomes possible to heat-treat the steel. With heat treatment, the stainless gets hardness. As a result, the steel becomes perfect to make surgical tools, knives, and cutting tools.
Unlike austenitic and ferritic grades, this stainless steel grade isn’t appropriate for stretching and drawing. It is hard and strong, but difficult and brittle to weld and form. The most common use cases include pocket knives, razor blades, plastic injections, ball bearings, and tweezers. 420 is a common example of this material type.
Three Tempers
It is possible to either heat-treat or cold-work all stainless steel grades to achieve the desired strength. Many stainless steel stamping manufacturers label the hardness of stainless still in the following ways:
Dead Soft: Completely annealed condition (maximum soft).
Quarter Hard: Partly heat-treated or cold worked, with a little strength and toughness increase.
Half Hard: Achieving greater hardness through further heat treatment or cold working, and great strength and toughness.
Three-Quarter Hard: Almost completely hardened. However, very tough and had a little malleability left.
Full Hard: Poor formability, but borderline brittle and fully hardened.
To perfectly form and cut stainless steel, it is essential to have a reliable understanding of the formability, hardness, and type. If you don’t know materials well, it will affect your process design in the wrong way.
What is Pressure Die Casting?
If you are after high-volume production, you should choose pressure die casting. It is also the most cost-effective and highly reliable process for net-shaped metal components with tight tolerances. Many China pressure die casting manufacturers inject molten metal alloys into the steel tool (or mold) under great pressure to complete the process of die casting. It gets hardened quickly, forming the net-shaped part. Then, it is extracted automatically.
Pressure Die Casting Benefits and Types
It costs low than other processes. Moreover, it is economical as you can produce millions of components before the replacement. It also ensures casting with a reliable surface finish and closer dimensional control. It is also possible to achieve thin walls castings, and therefore they are also lightweight.
There are two types of pressure die casting; high pressure and low pressure. High pressure is the most used type with approximately 50 percent of all casting productions of light alloys. On the other hand, the low pressure accounts for approximately 20 percent of the entire production. However, the use of low-pressure type is on the rise.
The high-pressure type is suitable for castings with detailed geometry and tight tolerance requirements. On the other hand, the low-pressure type is an ideal choice for non-critical and larger parts. Machine dies and the machine itself is extremely expensive. Therefore, the pressure die is suitable only when you are after high-volume production.
Let’s take a deeper insight into the two die casting types for a better understanding.
In this type of die casting, manufacturers inject liquid metals with high pressure and high speed into metal molds. The basic gear consists of a couple of vertical platens. They place bolsters on platens, holding die halves. One of the platens is movable, while the other one is immovable. It allows the bending die to close and open.
Metal, in a certain amount, is drizzled into shot sleeves. Afterwards it is introduced into mold cavities. The hydraulically-driven piston helps complete this function. After metal solidification, the die opens and eventually, the casting removes.
The high pressure die casting has two different types. Let’s take a closer look at both.
1. Hot Chamber Procedure
This procedure is valid only for alloys with low melting points, including zinc that doesn’t erode and affect metal pots plungers, and cylinders. For casting, molten metals are positioned into a holding furnace. It requires a specific temperature nearby the machine. A holding furnace holds the mechanism of the injection. Most of it is constantly touching molten metals.
An injection piston transmits the pressure to force the metal into the bending die via gooseneck. For another shot, metals are sent towards the gooseneck on another stroke. With this procedure, there is the least contact between the metal you want to inject and the air
2. Cold Chamber Procedure
We don’t have to submerge injection systems in molten metals, making it a different procedure than the hot chamber. In contrast, the metal transfers via a ladle, automatically or manually. A hydraulic plunger helps push metal into the bending die. With this process, the contact duration between molten metals and injector parts is at a minimum. As a result, it helps in maximizing the component life.
However, entertaining the air into metals usually linked with the high-speed injection may result in gas porosity within the casting. We can obtain over 70,000KPa or 10,000psi injection pressures in a cold-chamber machine. This is a perfect method to produce steel castings with copper and aluminum alloys.
Low-Pressure Die Casting
Low pressure die casting is the appropriate casting procedure if you are after the most reliable castings of aluminum alloys with low melting alloys, including magnesium. Aluminum castings in 2kg to 150kg weight are normal features. First, we position the metal die above the sealed furnace that contains the molten metal. Then, a refractory-lined riser emerges into molten metals from the die’s bottom.
After that, the introduction of the air with low pressure (2-15psi, 15-100KPa) occurs into a furnace. As a result, molten metals enter the cavity of the die by rising with low turbulence. The pressure of the air is released once the metal solidifies. Due to this, the molten metal in a riser tube goes into the furnace. The casting extracts once the die opens after the subsequent cooling.
It is possible to evade the riser requirement by ensuring the appropriate die design. The reason behind it is the casting’s directional freezing. After the establishment of the sequence, you can control the process automatically through pressure controllers and temperature. It helps in overseeing the multiple die casting machines operation.
Casting the yield is remarkably high since there are normally no feeders and just one ingate.
Pressure Die Casting Use cases
Take a look at the following use cases of the pressure die casting:
- Aerospace castings
- Housings of electric motors
- Electronic industry cabinets
- Kitchenware, like a pressure cooker
- Hardware appliances, such as plumbing parts and pump parts
It is also suitable for automotive parts, such as manifolds, cylinder heads, blocks, wheels, etc.
CNC Bending and CNC Forming
It is a process to re-shape metals with the help of machine presses, including brake presses. With computerized-numerical-control (CNC) presses this process becomes precise and versatile. It is also possible to automate it with CAM/CAD drawings to achieve better efficiency in minimum lead times. CNC machining and bending involve the implementation and development of special computer programs for controlling presses operations. It results in enhanced accuracy in the final product.
The CNC bending process involves programming press brakes for accepting metal sheet part plane bank at certain distances by the area where the bend formation will occur. Press brakes fundamentally clamp workpieces between the punch and matching die. A press brake’s sides consist of a couple of C-frames. These C-frames connect to the table’s bottom and upper beam’s top tool.
CNC Bending and CNC Forming Advantages
CNC bending machine manufacturers opt for CNC bending/forming for various reasons. It helps ensure the best performance while facilitating enhanced control and precision. You can achieve high-accuracy bending in sheet metal by using high-quality bending equipment. Therefore, it is essential to buy the best quality equipment from a reliable aluminum CNC bending machine manufacturer. Moreover, it also minimizes the chances of damaging the workpiece through the wrong fit.
Metal bending with CNC can also work with multiple smaller parts and large workpieces. Consequently, there will be reduced delivery times and better production efficiency. Therefore, you can ensure that your projects complete within your budget and on time.
CNC bending/forming is known widely for its automation benefit. The comprehensiveness of the CNC allows you to avoid many other machines that need more human interaction and time, such as shaping machines, vertical millers, routers, and center lathes.
This process requires less space. Moreover, it also allows for economical and faster working. Many other machines require regular upkeep and acquisition. However, you can avoid this hassle if you choose CNC bending. Additionally, you will also save more money for extra personnel because you will need just one operator to program/supervise various CNC machines.
Various CNC bending machine suppliers are available on the market. Therefore, you must choose the most reliable one to buy your CNC machines to ensure quality. You can also outsource a CNC bending machine factory or service provider to create a more efficient, streamlined production cycle.
CNC Bending/Forming Use Cases
High-quality CNC forming/bending equipment helps in providing a reliable solution for all material types, scope, and project sizes. For instance, RV manufacturers can manufacture the best-quality vehicle panels for vehicles. The automotive industry is using it for utility truck tool drawers. Moreover, CNC bending/forming is also an ideal choice to make lifting equipment, like truck cranes, boom components, and frame rails.
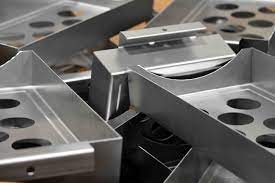
If you are using machine tools, such as a router, lathe, mill, or grinder for metal bending, you can replace it with CNC machines. These CNC metal sheets can perform metal fabrication jobs that need various cuts quickly at higher speeds. It is also possible when you need multiple angles or when your material is quite challenging. With CNC, you will ensure higher accuracy and fewer errors with minimum effort.
Specialized Capabilities
Some other metal bending capabilities include electronic and electrical products. Such products include control boxes, enclosures, light fixtures, computer cassis precision panels, and electrical cabinets. Appliance panels and doors, and refrigeration equipment are some other use cases of CNC bending/forming.
It is also possible to produce furnishings, like metal desks and cabinets, drawers, lockers, shelving, and doors. The construction industry is also getting benefits from it. Ceiling systems and floors for offices, distribution centers, manufacturing facilities, stores, and homes are some common examples. So CNC bending service can benefit almost every industry where metal parts are required.
CNC Bending Techniques
CNC bending involves two techniques or methods. The first technique uses press brakes connected to the lower bed. Engineers utilize V-block tooling for the appropriate metal position and the higher beam goes through the V-blade tool’s force. It is known as ‘down forming’.
In the second procedure, it is a complete contrast, when the up-forming machine goes through the lower ben, while the higher beam sits in the place. We achieve a similar result with both approaches. Therefore, engineers have unlimited options for designs.
You can program press brakes to handle several metal sheet parts. Programmable backstops define the back flat distance. Dependable engineers program V-blades also, where V-blocks are critical for the bend angle in metals. The penetration of the V-block through the V-block affects the final product.
The positioning of the CNC program unites several bend angles and lengths with the metal sheet. It determines the angles and positions for all sheet metal pieces. The computerized numerical controls press brakes define the sheet metal piece length that you can bend.
The thickness of the material is lined up with the tonnage and tensile strength of the material that a machine can work with. The size of the metal sheet gauge depends on the lower V-block’s opening size. Remember that a more open V-block means a wider internal bend radius.
Diffusion Welding
Also called ‘diffusion bonding’, diffusion welding can be the solid-state welding approach for metalworking purposes. It is an ideal strategy to join different and also comparable metals. It is based on the solid-state diffusion guidelines which demonstrate that particles of two metallic, solid surfaces strew with time.
Ordinarily, it often ends at the hoisted temperature of approximately 50% to 75% of the material’s super dissolving temperature. It is a common strategy for welding the lean metal’s thwart rotating layers and metal filaments or wires.
It is a popular strategy to join hard-heated metals and high strengths inside the atomic and aerospace businesses. Let’s go through a few diffusion welding types.
1. Solid-State Diffusion Welding
Diffusion bonding (welding) occurring in their rigid condition can be a knob to create solid links by arranging the bond. It can result in the coupling surfaces’ termination because the adjacent plastic may misshape when warm. It assists inter-diffusion at the joining fabric sheets’ exterior. Solid state diffusion welding is a common practice in many industries for welding.
2. TLP Diffusion Welding
The liquid-state diffusion bonding is based on the fluid stage arrangement at the line of the bond amidst isothermal bond cycles. The stage of fluid imbues the main fabric. It cements inevitably after the solute’s dissemination into the majority fabric. This procedure is known as TLP diffusion bonding.
Auto-Vacuum Welding: A couple of solid metals join through pressure in this strategy. It is also known as ‘pressure joining.
HIP: HIP (hot-isostatic-pressing) is the fabricating handle. It is useful in diminishing metals’ porosity with the assistance of diffusion welding, plastic misshaping, and crawl.
There are also a few other strategies apart from the above discussed. These include laser welding, forge welding, and electron beam welding.
Pros and Cons of Diffusion Bonding or Welding
There are various benefits along with some possible downfalls of using diffusion bonding. Let’s take a quick look at its pros and cons.
Pros
- The reinforced diffusion welding materialsexhibit similar mechanical and physical properties as base fabrics.
- Reinforced surfaces were tested via pliable testing.
- Diffusion bonding ensures clean joints. Joints are of high quality and there is no porosity and brokenness.
- You can join disparate and comparable materials with diffusion bonding. Because of this, it is high in demand.
- Because of exceptional measurement resilience, it is a perfect choice to deliver complex shapes and accuracy.
- Due to plastic distortion, there is a decrease in beneath diffusion.
- It is a simple method to approach and there are no running expenses.
Cons
- Even there are no running expenses, the initial setup will cost high.
- Diffusion bonding takes a lot of time.
- Workpieces plans are basic and somewhat tough.
- The accessible equipment limits the weld estimate.
- There is no use case for diffusion bonding in mass production.
- The result will be intensely subsidiary to welding parameters, such as temperature, fabric wrap-up, welding material, and weight.
Use Cases of Diffusion Bonding
There are many use cases of diffusion bonding or welding. Atomic diffusion welding is a classic example in the atomic industry. The aviation industry also uses this technique bonding factory materials. It is also suitable for welding beryllium, zirconium, and titanium metals as well as their alloys. Diffusion bonding can also bond nickel combinations, such as Udimet and Inconel. Another utilization of diffusion welding is bonding disparate metals, like Cu-Ti and Cu-AI, etc.
Ultrasonic Welding
Ultrasonic bonding has its use in workpiece liquefying through ultrasonic vibration touch warm and using the warm grinding vitality. The warm vitality depends on the workpiece responding development on other surfaces with specific sufficiency or relocation under a specific weight.
After a desired heat holding degree comes, the vibration halts, while there will be a specific weight on workpieces simultaneously. Such workpieces cool and set warm components to shape an adjacent bond.
Friction Welding
It is also known as ‘FRW’. It can be the solid-state welding approach to create warmth through automated grinding among work parts. The plastically upset (sidelong drive) is growing to merge and diminish fabrics. No dissolving occurs, so grinding bonding isn’t the fusion welding technique.
However, the solid-state bonding strategy is much similar to forge welding. It has its use with thermoplastics and metals in an array of car and flying applications. This type of welding is useful to work with wood.
Forge Welding
Also known as FOW, forge welding is an inelastic welding strategy. It joins two fabric parts by providing warmth up to a specific temperature. It may also comprise constraining and warming metals alongside presses, making adequate weight for plastic misshaping.
If you want to link fabrics, then this is the only method you can use. It is a flexible strategy you can use to join different and comparable metals. Transformation, mechanized forge, and manual forge welding can be the most common handle for fabrication.
What is High Precision CNC Machining?
In the industry, high precision CNC machining normally refers to components with some micrometer’s tolerances. Precision machining procedure states several machining procedures whose surface finish and machining accuracy are greater than parallel machining procedures.
The processes of precision machining include high-brightness and high-brightness grinding and precision cutting. Generally, the precision machining accuracy is 10~0.1μm, the Ra surface roughness is under 0.1μm, and the level of tolerance is more than IT5.
Precision machining’s real art is the blend of human engineering and computer control design. It can create high output and unique functions via the development of chemical control, fluid dynamics, extreme weather, machinery, and the longevity needed by the latest hardware and technology.
High precision CNC machining part factory engineers consider precision machining very critically to manufacture parts and tools in a stable and precise manner. They ensure that they can repeat the process with accuracy, durability, and consistency.
Precision Machining Applications
The precision machining process is useful when you want to remove material from the original item or product for making the end product. You can use it to create an array of items, parts, and products for various materials and objects. These parts normally need strict tolerance changes among the nominal parts and size. It means that the margin for error is very low in the parts’ production.
It is useful for composing many small and large objects as well as components in daily lives. If an object composition involves several small components, it normally requires precision machining for ensuring that it fits together precisely and operates properly.
Parts, finished products, and components designed for maintaining high durability and tight tolerances are deciding factors for using precision CNC machining. For instance, parts that must work simultaneously like machine components may require aligning within a specific range of 0.01-0.005mm. Precision machining and engineering not only ensure accurate parts manufacturing, but they also help produce parts repeatedly with precision.
Repairing components and tools might as well be another common use case of precision engineering. With time, the components or tools of an object might need welding, grooving, or machine calibration for restoring them to the original condition. A high precision CNC machining part manufacturer always knows its importance. This is again something that they can achieve through precision machining.
Moreover, precision machining also plays an essential role in automating production lines or test fixtures, particularly in high-precision industries. Automotive, medical equipment production lines, automation industry, and electronic industry are a few prominent examples.
Precision Machining: Materials and Essential Tools
High precision CNC machining suppliers use several raw materials for precision CNC machining. Those may include plastics, stainless steel, titanium, metals, steel, tungsten, steel, etc. For complex raw material removal and precise cutting, several tools are available. A diffusion welding rod is one of the essential tools in the industry. These tools are dependent on different raw materials. You can use milling machines, grinders, lathes, and various CNC machines for many materials.
All of them are CNC-controlled machines that a highly experienced and qualified operator can operate. These tools have unique functions. Therefore, parts size, parts complexity, surface treatment, materials, etc. decide which tool(s) you should choose.
What are the Different Types of Machines?
For the most optimal precision machining results, it is essential to follow certain blueprints accurately. CAD (computer-aided design) or CAM (computer-aided manufacturing) procedures are helpful in this regard. You can use CAM or CAD for creating 3D drawings essential for producing parts. It is essential to ensure that well-trained technicians create files according to exact specifications. After that, the CNC machining picks the CAM or CAD file for obtaining optimal results during the machining procedure.
To high precision CNC machining part suppliers or manufacturers, these high-precision and complex parts, complex machinery is essential for effectiveness. Below is the list of the different CNC machine type capabilities:
- 3-axis CNC machining
- CNC turning
- CNC milling
- Wire EDM and EDM
- 5-axis CNC machining
- CNC indexed machining 3+2-axis
- Precision grinding
Quality holds significant importance in precision machining. Therefore, an inspection machine also plays a critical role. Normal includes:
- Microscope
- CMM
- Calipers
- Micrometer
- Hardness checking machine
- Altimeter
Precision Machining Benefits
There are various benefits of precision machining. Let’s take a closer look at the most important ones.
Operational Efficiency
The process of precision machining depends largely on automatic CNC machines capable of running at higher speeds without manual interventions. It means that most China pressure die casting suppliers and manufacturers would require less labor for processing parts. It also results in minimum productions costs, while enhancing product quality. As a result, it can enhance the factory floor’s operational efficiency. However, operating complex systems and machines require experienced and skilled labor.
Increased Speed
Equipment that utilizes animated computer drawings for interpreting blueprints and executing them accordingly is an essential part of precision machining. Such machines can overtake humans for accuracy, overall output, and speed. Most significantly, machines don’t require sleep. They can operate for many hours.
Steady Product Quality
High precision CNC machining tools ensure steady output time. Consistent production of high-quality products or parts builds customer confidence while increasing brand visibility. Therefore, it is another massive benefit you will get with precision machining.
Minimum Risk Factors
Mechanical or human errors increase the costs of production and slow down the whole production process. However, we can use smart machines to eliminate human errors. Computers follow predefined operations very strictly. Therefore, there are almost no chances of them going wrong.
Low Error
CNC machining tools will implement an automated machining process after you provide precise specifications. The probability of errors is very low when we compare it with manual processing.
Minimized Production Costs
Usually, we use CNC machines for manufacturing precision parts. This manufacturing procedure has a comprehensive nature. Therefore, it reduces waste, errors possibility, and labor. Because the productions costs are low, automated systems are rising in popularity in the manufacturing field.
Fast Production
Last but not the least; fast production is another huge advantage that comes with CNC machining. Fast automatic manufacturing machines can perform tasks repeatedly with high accuracy. Humans cannot compete with precision engineering when we talk about accuracy and speed. The less turnaround time assists companies to attain sustainable growth and meet their market expectations.
Final Words
High precision CNC machining is playing a great role in the manufacturing industry. Various industries are using CNC machining for tasks like stainless steel lost wax casting. Aerospace & optics, automotive, transportation, and military are the most prominent industries using CNC machining. It ensures fast production, minimum risk factors, steady product quality, and improved speed and efficiency.